Local Rust Removal for Sheet Metal
(1) Brushing Method for Rust Removal
The brushing method uses a flexible steel wire or copper wire brush to scrape off rust, oxide layers, and dirt from the metal surface. This can be done manually or by using an electric tool, like a grinder. Here’s how to remove rust using an electric grinder:
- Remove the grinding disc from the electric grinder and replace it with a wire brush. Tighten it according to the specified torque.
- Ensure the grinder’s switch is off before plugging it into the socket.
- Hold the grinder with both hands, position it in front of your body, and face the area to be polished. Bring the grinder close to the surface of the metal.
- Press the switch, and move the grinder toward the surface at an angle of about 15°. Use your wrist to apply light pressure so the wire brush firmly contacts the metal surface to cut and remove rust.
- Move the grinder in a back-and-forth or side-to-side motion until the entire surface is polished and rust-free.
- Turn off the power switch and wait until the wire brush completely stops rotating. Then unplug the grinder and store it properly.
(2) Grinding Method for Rust Removal
Manual rust removal using sandpaper is similar to sanding off old paint. For mild rust, a grinder with #60 sandpaper can be used in a similar way to removing old paint. For more severe rust, a grinding wheel can be directly used to remove the rust.
Methods for Removing Rust from Entire Metal Sheets
(1) Tumbling Method for Rust Removal
The tumbling method uses a rotating drum filled with abrasive materials and metal parts. Driven by a motor, the parts continuously tumble and rub against the abrasive materials, which removes burrs, oxide layers, and rust that form during casting or stamping. Compared to polishing or grinding, this method reduces production costs and increases efficiency. Tumbling is also known as sand blasting.
(2) High-Pressure Water Rust Removal
High-pressure water rust removal uses the impact force of high-pressure water jets to remove rust. This is an advanced rust removal technique, suitable for cleaning large metal surfaces, removing rust, oxide layers, and old paint. This method requires specialized equipment. When applied in highly automated environments, high-pressure water rust removal offers high efficiency and low cost. Common pressures for continuous water jets range from 20 to 80 MPa.
(3) Sandblasting Method for Rust Removal
The equipment and operation methods for sandblasting rust removal are similar to those for removing old paint.
Dry Sandblasting:
There are several types, including suction, pressure, gravity, and centrifugal methods. The most commonly used in industries are suction and pressure methods. Suction equipment is simple but less efficient, making it suitable for small parts. Pressure equipment is larger, more powerful, and highly efficient, ideal for medium and large parts and large-scale production.
Wet Sandblasting:
There are three common methods: mist sandblasting, water-air sandblasting, and water sandblasting. Wet sandblasting mixes a specified amount of water and rust inhibitors with the abrasive to form a sand-water mixture. This method reduces the impact of abrasive on metal surfaces, minimizing metal removal and producing finer surfaces. The working principles and characteristics of wet sandblasting are shown in Table 4-1.
The working principles and characteristics of wet sandblasting.
①Atomized sandblasting:
- Principle:That is, low-pressure atomized sandblasting, where the sand is sprayed from a compressed air system equipped with a venturi to the nozzle, impacting the surface of the part with an atomized water-sand stream.
- Features:The roughness of the blasted surface can only be changed by changing the abrasive particle size.
②Water Sandblasting:
- Principle: Sandblasting using a water-sand stream without compressed air.
- Features: The surface roughness can only be changed by adjusting the water pressure.
③Water-Air Sandblasting:
- Principle: A slurry pump delivers the water-sand mixture at high pressure through a hose to the nozzle, where compressed air is introduced. The high-speed water and sand stream impacts the surface of the part.
- Features: The surface roughness can be adjusted by changing the compressed air pressure.
3.The most suitable surface treatment method is water-air sandblasting. The abrasive used is aluminum oxide (Al2O3), which has the advantage of not easily breaking down. It can be recycled, improving working conditions and reducing pollution. Silicon carbide and zirconium magnesium sand can also be used, but they are rarely adopted due to their high cost.
More sandblasting processes
When wet sandblasting cannot be used, dry sandblasting is selected based on the shape and structural complexity of the part. In this case, the parts must be dry, and the abrasive should be dried or sun-dried. The air pressure for dry sandblasting is determined by the material, structural shape, thickness, and the machining allowance of the part. If the part is less than 3mm thick, sandblasting is not recommended. This is because thin parts are prone to deformation. Instead, manual or mechanical grinding should be used. For parts thicker than 3mm, sandblasting can be applied.
Dry sandblasting can be done in two ways: intermittent and continuous. Intermittent sandblasting takes place in a closed or open sandblasting area and is used for large parts. Its advantage is that it can reach complex shapes, but the labor intensity is high, and efficiency is low.
The process for dry sandblasting is as follows:
Degreasing → Dry Sandblasting → Cleaning → Phosphating → Cold Water Rinse → Hot Water Rinse → Air Dry or Blow Dry → Primer Application.
The process for wet sandblasting is basically the same as dry sandblasting. After dry sandblasting, the surface will be an even, matte gray (sandblasted finish). It must meet the surface treatment level specified in GB/T8923.1-2011 for “Visual Assessment of Surface Cleanliness Before Coating – Part 1: Rust Grades and Preparation Grades of Uncoated Steel Surfaces and Steel Surfaces after Complete Removal of Existing Coatings.”
After wet sandblasting, the surface will be uniform, dense, and either matte or semi-matte gray. The requirements are the same as for dry sandblasting. The typical working pressure for sandblasting is between 0.04–0.56 MPa. Wet sandblasting usually uses 0.56 MPa. The size of the sand particles and the air pressure are shown in Table 4-2.
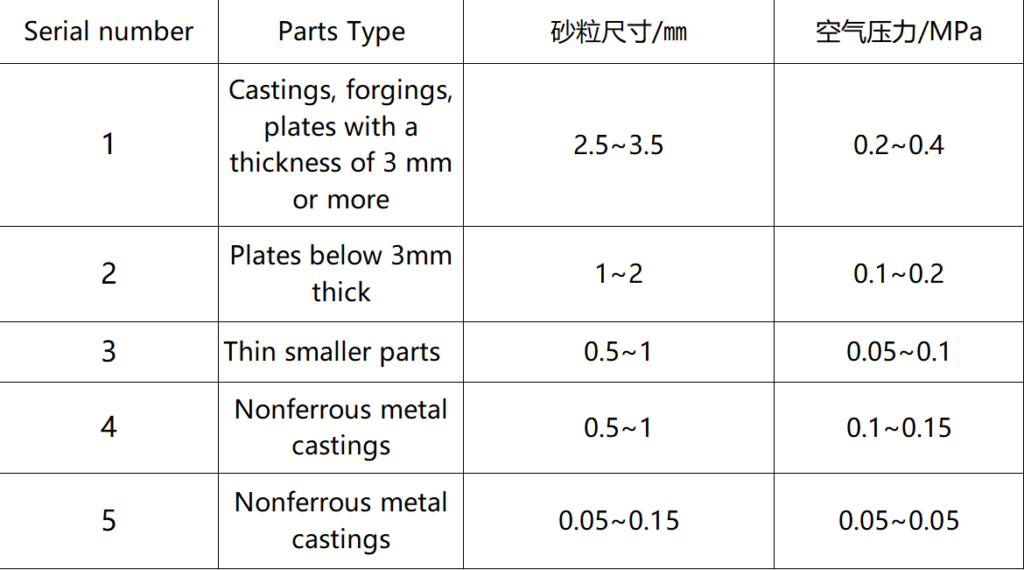
(4) Shot Blasting Rust Removal
The working principle of shot blasting is that pellets are thrown from a rotating impeller. The pellets are shot onto the surface at a speed of 80m/s, delivering 130kg/min of material in a fan-shaped stream. Shot blasting equipment can be intermittent or continuous. Productivity can be improved by adjusting the blade direction, increasing the flow density of the shot, and enlarging the treatment area. Fixed shot blasting equipment is highly automated but is mainly used for surface treatment of plates and profiles.
Before shot blasting, parts should be preheated to 40-45°C. This removes moisture from the metal surface and shortens drying time after painting. The pellet size for removing rust and oxide layers is 0.5-1.5mm. Smaller pellets may not fully remove the oxide layer, while larger ones create an uneven rough surface, affecting the quality of the coating.
(5) Chemical Rust Removal
Chemical rust removal includes acid pickling, combined rust removal, alkaline rust removal, electrolytic rust removal, pollution-free rust removal agents, and ultrasonic cleaning.
Acid Pickling Rust Removal: This method uses acids to react with rust (iron oxides) on the metal surface, forming water-soluble salts that are easily removed.
Combined Rust Removal: This involves degreasing and rust removal in one liquid bath. It includes “one-step” degreasing and rust removal, “three-in-one” degreasing, rust removal, and phosphating, and “four-in-one” degreasing, rust removal, phosphating, and passivation. This method simplifies production, increases efficiency, reduces the size of equipment and space requirements, and saves water and materials. Weak phosphoric acid solutions lower the risk to humans and the environment.
Alkaline Rust Removal: This method uses alkaline solutions to dissolve rust.
Electrolytic Rust Removal: In this method, the part is immersed in an electrolyte, and a direct current is applied. The rust is removed through an electrochemical reaction.
Pollution-Free Rust Removal Agent: This method is widely used in developed countries. It breaks down the oxides on the metal surface and removes rust. This process prevents further oxidation by forming a passivation layer. It also provides a clean surface for painting or electroplating without altering the metal’s precision or properties.
(6) Ultrasonic Rust Removal
Ultrasonic cleaning equipment consists of a cleaning tank and an ultrasonic generator. The generator includes a power source and a transducer.
The power source converts low-frequency electricity (50Hz) into high-frequency electricity (over 20kHz) and sends it to the transducer. The transducer’s piezoelectric elements turn the electrical energy into high-frequency vibrations. Although the vibrations are small (just a few microns), they generate high acceleration. When multiple transducers are activated with the same frequency and voltage, a powerful invisible piston is formed, vibrating at high frequencies. In a liquid medium, this causes cavitation, which impacts and peels off surface contaminants such as oil and oxide layers, achieving rust removal.