When you think about the tools that shape the modern world—cars, airplanes, smartphones—you might not immediately think of CNC Milling Machines. But here’s the thing: these machines are the unsung heroes behind so many of the precision parts we rely on every day. From the engine blocks in your car to the circuit boards in your phone, CNC mills are quietly shaping the world around us. So, let’s take a closer look at what makes these machines tick, why they’re so important, and how they’re evolving to meet the demands of modern manufacturing.
What Exactly is a CNC Milling Machine?
At its core, a CNC Milling Machine is a computer-controlled tool that uses rotating cutting tools to remove material from a workpiece. Unlike a lathe, which spins the workpiece, a mill moves the cutting tool around the workpiece to create complex shapes and features. This makes it perfect for everything from prototyping to mass production.
Why Should You Care?
- Precision: These machines can achieve tolerances as tight as ±0.001 inches (0.025 mm). That’s thinner than a sheet of paper!
- Efficiency: They’re automated, which means fewer mistakes and faster production.
- Versatility: Whether you’re working with aluminum, steel, or even titanium, a CNC mill can handle it.
The Key Parts of a CNC Milling Machine
To really understand how a CNC mill works, let’s break it down into its main components. Think of it like a team—each part has a specific role, and they all work together to get the job done.
1. Spindle: The Powerhouse
The spindle is the heart of the mill. It holds the cutting tool and rotates it at high speeds to remove material from the workpiece. The spindle’s speed can be adjusted depending on the material and type of cut required.
- 行业冷知识: In high-performance mills, spindle speeds can reach up to 30,000 RPM. That’s fast enough to make the cutting tool look like it’s standing still!
2. Worktable: The Foundation
The worktable is where the workpiece is secured. It can move in multiple directions (X, Y, and Z axes) to position the workpiece under the cutting tool. Some advanced mills even have rotary tables for 4th and 5th-axis machining.
- Pro Tip: For precision work, the worktable can be adjusted to apply just the right amount of pressure, preventing the workpiece from moving during machining.
3. Tool Changer: The Multi-Tasker
The tool changer is like a Swiss Army knife for CNC mills. It holds multiple cutting tools and can automatically switch between them during the machining process. This means the mill can perform multiple operations—like drilling, milling, and tapping—without needing manual intervention.
- Example: A 24-station tool changer can handle everything from rough cutting to fine finishing in a single setup. Talk about efficiency!
4. Control Panel: The Brain
The control panel is where the operator inputs the G-code instructions that tell the machine what to do. Modern control panels often feature touchscreens and intuitive interfaces, making them easier to use than ever before.
- Cool Feature: Some advanced panels include simulation software, allowing operators to visualize the machining process before starting. This can help catch potential issues before they become costly mistakes.
G71粗车循环代码实例
Here’s an example of G71 rough turning cycle code for a CNC lathe (yes, lathes and mills share some similarities!):
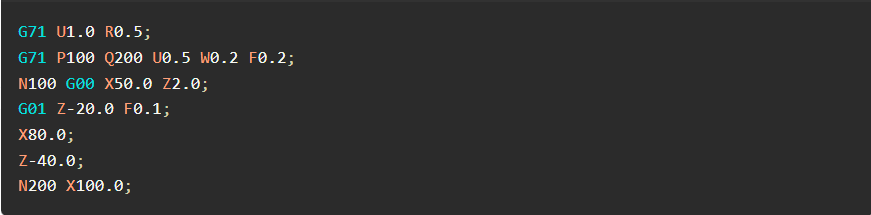
This code tells the machine to perform a rough turning operation with a depth of cut of 1.0 mm and a retract distance of 0.5 mm.
5. Coolant System: The Protector
The coolant system keeps the cutting tool and workpiece cool during machining. This not only extends the life of the tool but also improves the surface finish of the workpiece.
- Did You Know? Some coolant systems use high-pressure jets to remove chips from the cutting area, preventing them from interfering with the machining process.
How Do These Parts Work Together?
Here’s a quick rundown of how these components come together to create a finished part:
- Setup: The workpiece is clamped onto the worktable, and the appropriate cutting tools are loaded into the tool changer.
- Programming: The operator inputs the G-code instructions into the control panel.
- Machining: The spindle rotates the cutting tool, and the worktable moves the workpiece into position.
- Finishing: The machine performs multiple passes to achieve the desired shape and surface finish.
Why Are CNC Milling Machines So Essential?
1. Precision and Accuracy
CNC mills are known for their ability to produce parts with extremely tight tolerances. For example, in the aerospace industry, CNC mills are used to create turbine blades and engine components that require micron-level precision. According to a 2022 report by Aerospace Manufacturing and Design, CNC milling has reduced error rates in aerospace manufacturing by over 50%.
2. Speed and Efficiency
CNC mills can run 24/7 with minimal supervision, significantly speeding up production. A 2021 study by Modern Machine Shop found that companies using CNC mills saw a 30% increase in production efficiency compared to manual milling.
3. Cost-Effectiveness
While the initial investment in a CNC mill can be high, the long-term savings are substantial. By reducing material waste and labor costs, CNC milling can lower production expenses by up to 20%, according to a 2020 analysis by Manufacturing Global.
4. Flexibility
One of the biggest advantages of CNC mills is their ability to switch between different tasks quickly. With just a change in the G-code, the same machine can produce a car part one day and a medical implant the next.
Real-World Applications of CNC Milling Machines
1. Automotive Industry
CNC mills are used to create critical components like engine blocks, transmission cases, and suspension parts. For example, Tesla uses CNC mills to produce high-precision components for its electric vehicles.
2. Aerospace Industry
The aerospace sector relies heavily on CNC mills to create lightweight, high-strength parts. Boeing, for instance, uses CNC mills to manufacture components like wing ribs and fuselage frames.
3. Medical Devices
CNC mills are used to produce surgical instruments, implants, and prosthetics. A 2023 case study by Medical Design & Outsourcing highlighted how a medical device company reduced production time by 40% using CNC mills.
4. Consumer Electronics
CNC mills are used to create precision components for devices like smartphones and laptops. Apple, for example, uses CNC mills to produce the aluminum casings for its MacBooks.
Challenges and Limitations
1. High Initial Cost
CNC mills can be expensive, with prices ranging from $50,000 for basic models to over $500,000 for advanced systems. However, the long-term savings often justify the investment.
2. Skilled Labor Required
Operating a CNC mill requires specialized training. According to a 2021 article by IndustryWeek, there’s a growing skills gap in the manufacturing sector, with many companies struggling to find qualified CNC operators.
3. Material Constraints
While CNC mills can handle a wide range of materials, some (like hardened steel or titanium) require specialized tools and slower machining speeds, which can increase costs.
The Future of CNC Milling Machines
The future of CNC mills is looking bright, with several exciting trends on the horizon:
1. Automation and Robotics
The integration of CNC mills with robotic arms is revolutionizing manufacturing. For example, Fanuc has developed robotic systems that can load and unload CNC mills, further reducing labor costs and increasing efficiency.
2. AI and Machine Learning
Artificial intelligence is being used to optimize CNC milling operations. A 2023 report by TechCrunch highlighted how AI algorithms can predict tool wear and adjust machining parameters in real-time, reducing downtime and improving accuracy.
3. Additive Manufacturing (3D Printing)
While CNC mills are subtractive machines, they’re increasingly being combined with additive manufacturing. Hybrid machines that can both 3D print and CNC mill are becoming more common, offering the best of both worlds.
Wrapping It Up
CNC milling machines are the backbone of modern manufacturing, enabling the production of high-precision, complex components with unmatched efficiency. From cars to medical devices, these machines play a crucial role in shaping the world around us. While they come with challenges like high costs and the need for skilled labor, the benefits far outweigh the drawbacks.
If you’re considering investing in a CNC mill, it’s important to weigh your options carefully. Look for a machine that meets your specific needs, whether it’s a basic 3-axis mill or a high-end 5-axis system. And don’t forget to factor in the cost of training your team to operate it effectively.
At the end of the day, a CNC mill isn’t just a tool—it’s an investment in the future of your business. So, what will you create with it?
References
- Aerospace Manufacturing and Design (2022) – Report on CNC milling in aerospace.
- Modern Machine Shop (2021) – Study on production efficiency with CNC mills.
- Manufacturing Global (2020) – Analysis of cost savings with CNC milling.
- IndustryWeek (2021) – Article on the skills gap in CNC machining.
- TechCrunch (2023) – Report on AI in CNC milling operations.
- Fanuc Robotics – Information on CNC mill automation.