The Anodizing process enhances metal surfaces by creating a durable, corrosion-resistant finish. Various industries, including aerospace, automotive, and electronics, rely on anodized materials for their superior properties. Anodizing aluminum, in particular, improves durability, wear resistance, and aesthetic appeal. This blog aims to provide a comprehensive understanding of the principles and applications of anodizing, highlighting its significance in modern manufacturing and design.
Understanding Anodizing
Definition and Overview
What is Anodizing?
Anodizing enhances metal surfaces through an electrochemical process. This process converts the metal surface into a durable, decorative, and corrosion-resistant anodic oxide finish. Industries often use anodizing to improve corrosion resistance on aluminum alloys. The anodized layer provides a protective barrier, preventing moisture and corrosive elements from penetrating the metal.
Historical Background
Anodizing’s roots trace back to the early 20th century. Pioneering work during this period set the stage for modern anodizing techniques. Early applications focused on improving the durability and corrosion resistance of aluminum parts. Over time, advancements in technology expanded anodizing’s applications across various industries.
Basic Principles
Electrochemical Process
The anodizing process involves immersing the metal in an electrolytic solution. An electric current passes through the solution, causing oxidation on the metal’s surface. This controlled oxidation forms a thick, protective oxide layer. The thickness and properties of this layer depend on the process parameters.
Role of Electrolytes
Electrolytes play a crucial role in the anodizing process. Common electrolytes include sulfuric acid, chromic acid, and phosphoric acid. Each electrolyte type affects the characteristics of the anodized layer. Sulfuric acid is the most widely used due to its efficiency and cost-effectiveness.
Types of Anodizing
Different types of anodizing processes exist to meet specific requirements:
- Type I (Chromic Acid Anodizing): Provides excellent corrosion resistance and is suitable for aerospace applications.
- Type II (Sulfuric Acid Anodizing): Commonly used for general-purpose applications, offering good corrosion resistance and dyeing capabilities.
- Type III (Hard Anodizing): Produces a thicker and harder oxide layer, ideal for wear-resistant applications.
Materials Suitable for Anodizing
Aluminum
Aluminum is the most commonly anodized material. The process significantly enhances aluminum’s wear and corrosion resistance. Anodized aluminum finds applications in aerospace, automotive, and consumer products. The anodization process also allows for various color finishes, enhancing the aesthetic appeal of aluminum parts.
Titanium
Titanium anodizing creates a protective oxide layer on the metal’s surface. This layer improves titanium’s corrosion resistance and biocompatibility. Medical devices and implants often use anodized titanium due to its enhanced properties.
Other Metals
Other metals, such as magnesium and zinc, can also undergo anodizing. However, these metals require specialized processes and are less common than aluminum and titanium. Anodizing these metals can still provide benefits like improved corrosion resistance and surface hardness.
The Anodizing Process
Pre-Treatment
Cleaning
Cleaning removes contaminants from the metal surface. Oils, greases, and dirt can interfere with the Anodizing process. Technicians use alkaline or acidic solutions to clean the metal. This step ensures a uniform anodized layer.
Etching
Etching creates a rough surface on the metal. This step enhances adhesion during the Anodizing process. Common etching agents include sodium hydroxide for aluminum. The etching process also removes any remaining oxides.
Desmutting
Desmutting eliminates residues left from the etching process. These residues, often called “smut,” can affect the quality of the anodized layer. Technicians use nitric acid or other desmutting agents. This step prepares the metal for the anodizing stage.
Anodizing Stage
Setup and Equipment
The setup involves immersing the metal in an electrolytic bath. The bath contains an electrolyte solution, such as sulfuric acid. An electric current passes through the bath. This current initiates the Anodizing process. Specialized equipment controls the voltage and temperature.
Process Parameters
Process parameters determine the characteristics of the anodized layer. Key parameters include voltage, current density, and time. Higher voltages produce thicker oxide layers. Lower temperatures result in harder coatings. Technicians adjust these parameters based on the desired properties.
Quality Control
Quality control ensures the consistency of the anodized layer. Inspections involve measuring the thickness and hardness of the oxide layer. Visual inspections check for defects like discoloration or uneven surfaces. Quality control guarantees that the anodized product meets industry standards.
Post-Treatment
Sealing
Sealing closes the pores in the anodized layer. This step enhances corrosion resistance. Hot water or steam baths are common sealing methods. Some processes use chemical sealants for added protection.
Coloring
Coloring adds aesthetic value to the anodized metal. Dyes penetrate the porous oxide layer. The color becomes part of the metal surface. This step allows for a wide range of color options. The Anodizing process can produce vibrant and durable finishes.
Finishing Techniques
Finishing techniques improve the final appearance of the anodized product. Polishing creates a smooth and shiny surface. Brushing provides a textured finish. These techniques enhance both the look and feel of the anodized metal.
Applications of Anodized Materials
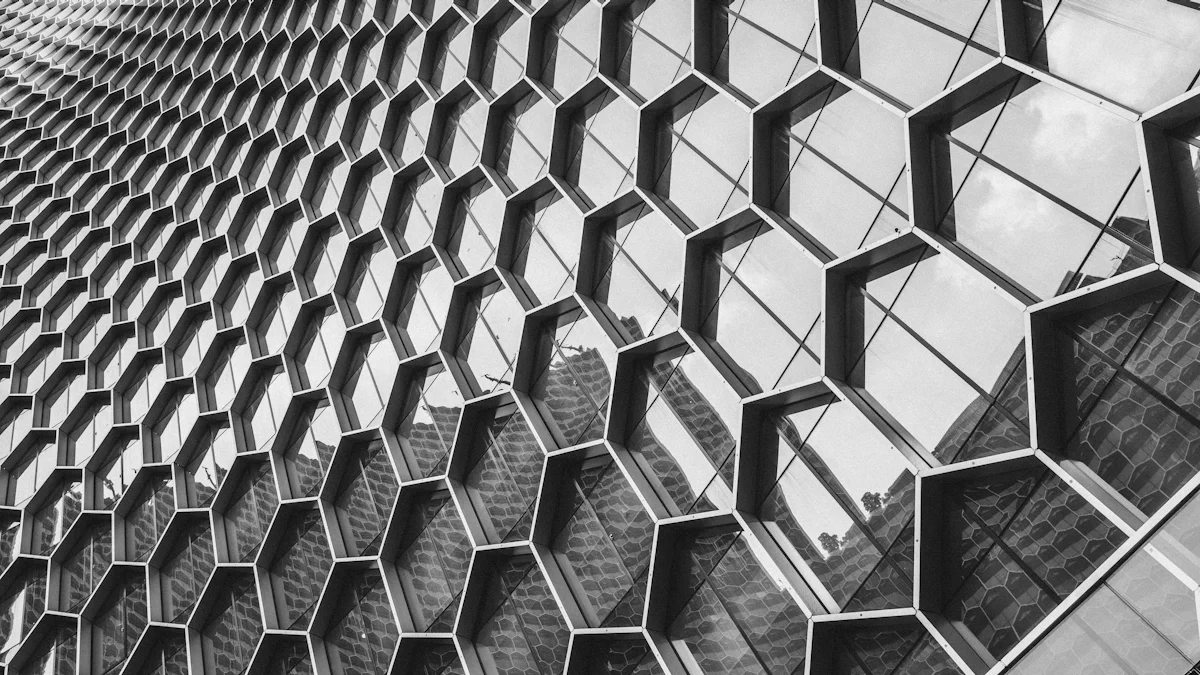
Industrial Applications
Aerospace
The aerospace industry relies heavily on anodized materials. Anodized aluminum offers excellent corrosion resistance and durability. These properties are crucial for aircraft components exposed to harsh environments. The Anodizing process enhances the lifespan of parts such as wings, fuselage panels, and landing gear. The lightweight nature of anodized aluminum also contributes to fuel efficiency.
Automotive
The automotive sector benefits significantly from anodized materials. Companies like Tesla use anodized aluminum extensively in vehicles. This approach achieves lightweight construction, superior strength, and exceptional corrosion resistance. Anodized aluminum also provides a premium appearance, enhancing the vehicle’s aesthetic appeal. The Anodizing process allows for various colors and finishes, reducing maintenance and replacement costs over time.
Electronics
Electronics manufacturers utilize anodized materials for several reasons. Anodized aluminum enclosures protect sensitive electronic components from corrosion and wear. The Anodizing process also improves heat dissipation, which is vital for electronic devices. Anodized surfaces offer an attractive finish, making them suitable for consumer electronics like smartphones and laptops.
Consumer Products
Household Items
Household items often feature anodized materials for enhanced durability and aesthetics. Cookware, such as pots and pans, benefits from the Anodizing process. The anodized layer provides a non-stick surface and resists scratches and corrosion. Anodized aluminum also appears in home appliances, offering a sleek and modern look.
Sporting Goods
Sporting goods manufacturers use anodized materials to improve product performance and longevity. Bicycles, golf clubs, and fishing reels often feature anodized aluminum components. The Anodizing process enhances these items’ resistance to wear and corrosion. Anodized surfaces also allow for vibrant colors, adding to the visual appeal of sporting equipment.
Fashion Accessories
Fashion accessories, including watches and jewelry, utilize anodized materials for their aesthetic and protective qualities. Anodized aluminum and titanium offer a wide range of color options. The Anodizing process ensures that these accessories remain resistant to scratches and corrosion. This durability makes anodized fashion items both stylish and long-lasting.
Architectural Uses
Building Facades
Architects favor anodized materials for building facades due to their durability and aesthetic versatility. Anodized aluminum panels resist weathering and corrosion, ensuring a long-lasting exterior finish. The Anodizing process allows for various color options, enabling architects to achieve unique and visually appealing designs.
Interior Design
Interior designers incorporate anodized materials to create modern and elegant spaces. Anodized aluminum and titanium can be used for fixtures, fittings, and decorative elements. The Anodizing process provides a durable and low-maintenance finish, making it ideal for high-traffic areas. Anodized surfaces also offer a sleek and contemporary look.
Structural Components
Structural components in buildings benefit from the strength and durability of anodized materials. Beams, columns, and other load-bearing elements often feature anodized aluminum. The Anodizing process enhances these components’ resistance to environmental factors, ensuring structural integrity over time. Anodized materials also contribute to the overall aesthetic of the structure.
Benefits and Disadvantages
Advantages
Corrosion Resistance
Anodized aluminum offers superior corrosion resistance. The anodizing process creates a thick, protective oxide layer on the metal surface. This layer prevents moisture and corrosive elements from penetrating the metal. Industries such as aerospace and automotive benefit significantly from this enhanced protection.
Aesthetic Appeal
Anodized materials provide a wide range of color options. The anodizing process allows dyes to penetrate the porous oxide layer. This results in vibrant and durable finishes. Anodized surfaces maintain their appearance over time, making them ideal for consumer products and architectural applications.
Durability
Anodized aluminum exhibits increased hardness and wear resistance. The anodizing process enhances the metal’s ability to withstand scratches and abrasion. This durability reduces maintenance and replacement costs over time. Anodized materials are suitable for high-traffic areas and demanding environments.
Disadvantages
Cost Considerations
The anodizing process can be costly. Specialized equipment and chemicals are required. The process parameters must be carefully controlled. These factors contribute to higher production costs compared to non-anodized materials. Small-scale projects may find anodizing less cost-effective.
Process Limitations
Anodizing is not suitable for all metals. Aluminum and titanium are the most commonly anodized materials. Other metals, such as magnesium and zinc, require specialized processes. These limitations restrict the range of materials that can benefit from anodizing. Additionally, the thickness of the anodized layer depends on the process parameters, which may not meet all application requirements.
Environmental Impact
The anodizing process involves the use of chemicals such as sulfuric acid. These chemicals pose environmental risks if not properly managed. Waste disposal and treatment add to the overall environmental footprint. Industries must implement stringent measures to minimize the environmental impact of anodizing.
Practical Considerations
Maintenance of Anodized Surfaces
Cleaning Methods
Proper maintenance of anodized surfaces ensures longevity and performance. Cleaning methods play a crucial role in preserving the quality of the Anodizing process. Use mild detergents and warm water for routine cleaning. Avoid abrasive cleaners that can damage the anodized layer. Soft cloths or sponges work best for wiping down surfaces. For stubborn stains, use a solution of water and vinegar. Rinse thoroughly to remove any residue.
Repair Techniques
Repairing anodized surfaces requires specialized techniques. Minor scratches can be polished out using fine abrasive pads. For deeper scratches, re-anodizing may be necessary. This involves stripping the existing anodized layer and reapplying the Anodizing process. Consult professionals for significant repairs to ensure the integrity of the anodized surface.
Choosing the Right Anodizing Process
Factors to Consider
Selecting the appropriate Anodizing process depends on several factors. Consider the type of metal and its intended application. Aluminum and titanium are the most commonly anodized materials. Evaluate the desired properties, such as corrosion resistance and aesthetic appeal. Process parameters, including voltage and electrolyte type, also influence the outcome. Consulting experts like Anne Deacon Juhl can provide tailored advice for specific needs.
Industry Standards
Adhering to industry standards ensures the quality and consistency of anodized products. Standards specify requirements for thickness, hardness, and appearance. Organizations like ASTM and ISO provide guidelines for the Anodizing process. Compliance with these standards guarantees that anodized materials meet performance expectations. Regular audits and inspections help maintain adherence to industry norms.
The Anodizing process enhances metal surfaces, providing durability, corrosion resistance, and aesthetic appeal. Industries like aerospace, automotive, and electronics benefit from anodized materials. Anodizing aluminum, titanium, and other metals offers significant advantages. The importance of anodizing in modern manufacturing and design cannot be overstated. Continued exploration of applications and innovations will drive further advancements. Embracing the potential of anodizing will lead to new opportunities and improved performance across various sectors.